Our take on PFAS – and why we can’t (yet) live without it in workwear
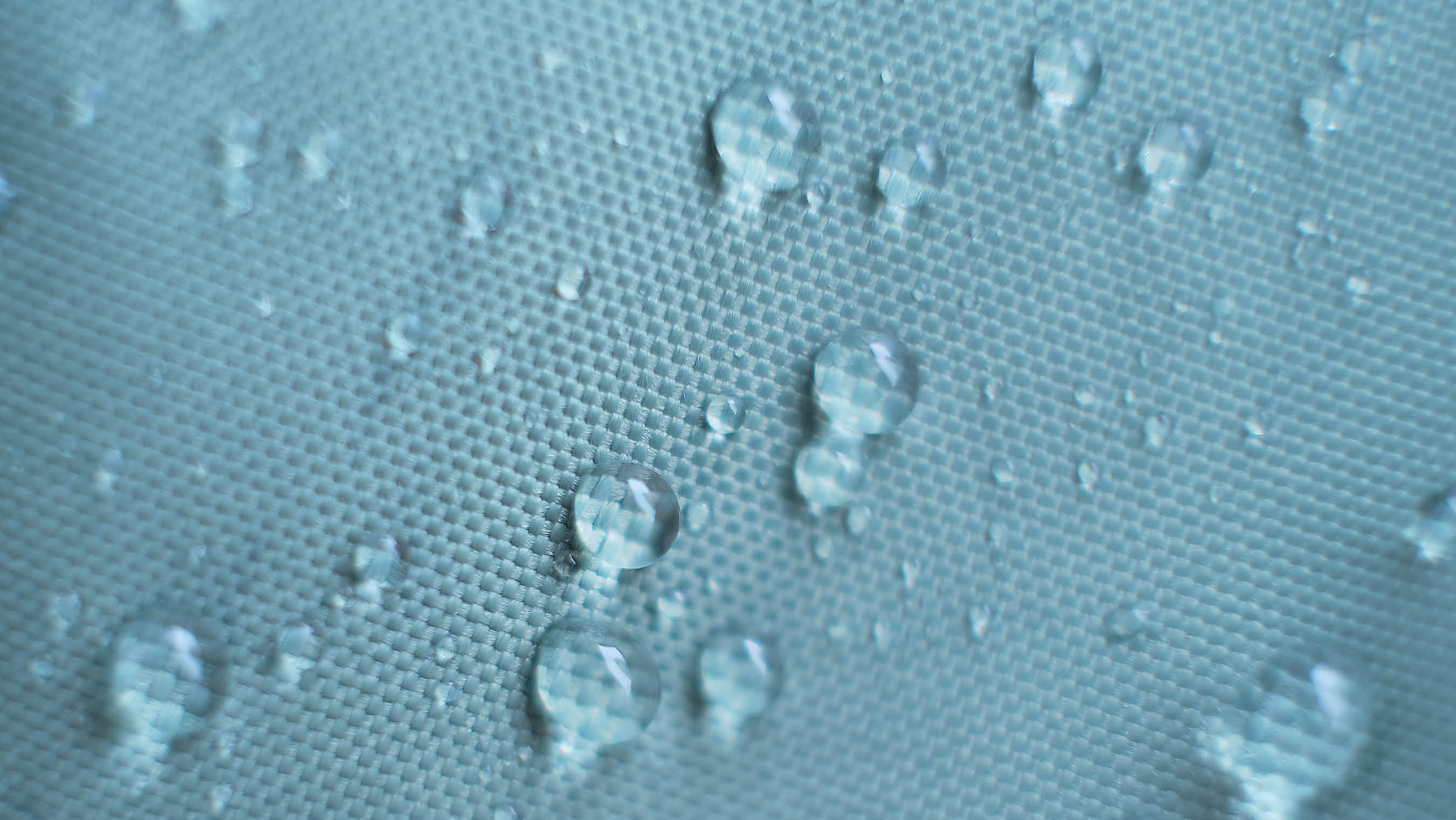
The European Union is working on a ban on PFAS due to their harmful effects on humans and the environment. According to the REACH proposal, a complete ban is scheduled for 2025. However, there is a notable exception: personal protective equipment (PPE) category III. Within this category – including EN13034:2005 + A1:2009, EN11612, and EN61482 – PFAS may be used until 2037 due to their proven protective properties.
What is PFAS?
PFAS is a collective term for poly- and perfluoroalkyl substances: synthetic chemicals known for their water-, oil-, grease- and dirt-repellent properties. They are used in various products such as cookware, cosmetics, packaging, firefighting foams and – relevant to our industry – clothing.
The problem? PFAS are nearly non-degradable and are found worldwide: in food, drinking water and even in the blood of polar animals. In textiles, PFAS are used in fluorocarbon finishes and ePTFE membranes, which are essential for repelling water-, oil- and chemical-based substances. But is it still viable to rely on them?
The basics: surface tension
Repellency starts with surface tension – the property that determines whether a liquid spreads out or beads on a surface. Oil and water do not mix simply because their surface tensions differ significantly.
Repellent finishes increase the surface tension of textiles, making it harder for liquids to penetrate. The lower the surface tension of a liquid, the harder it is to repel. For comparison:
Water: 72 mN/m
Olive oil: 32 mN/m
These values determine the required protection in the field.
PFAS and surface tension: what’s the difference?
Fluorocarbon finishes (PFAS) increase the surface tension of textiles to such an extent that they resist water-, oil- and chemical-based substances. So far, no alternative can match this performance.
However, not every risk requires PFAS. For water (which has a high surface tension), a PFAS-free solution is often sufficient. For oil and oil-based chemicals – with much lower surface tension – PFAS is still necessary for adequate protection.
Testing repellency: how does it work?
The most widely used test standard for chemical repellency is EN13034:2005 + A1:2009. This standard includes tests with substances like sodium hydroxide, sulfuric acid, xylene, and butanol. To be certified, a fabric only needs to successfully repel one of these substances.
But as we’ve seen, each liquid has a different surface tension. So the question arises: does this test offer sufficient certainty? If you need protection against various types of chemicals – with differing physical properties – EN14605 is a more reliable standard. Note: this standard is not part of our product range.
It’s all in the nuance
Is a PFAS-free finish useless then? Certainly not. The C0 finish, which is completely PFAS-free, provides solid protection against water-based chemicals.
A crucial note on the test method: the gutter test under EN13034 uses 10 ml of liquid (approximately two teaspoons) for 10 seconds. This shows it is a minimum standard. For many applications, that’s enough – and a PFAS-free finish will perform just fine.
Looking ahead: towards a safe and sustainable solution
From our perspective, we clearly distinguish between:
- Class 1: water-based substances
- Class 2: oil-based substances
These values are decisive for the necessary protection in the field.
Our approach:
Clothing that is not EN13034-certified and does not require oil repellency is being gradually transitioned to PFAS-free finishes.
For PPE category III garments, we assess whether oil repellency is required per use case. Where possible, we move towards sustainability. Where necessary, protection remains the top priority.
Want to know how this relates to FR-Treated versus Inherent? See our detailed explanation [here].
Back to practice: customer-driven choices
The decision to use PFAS or not is not black and white. It depends on the specific working conditions and chemical risks of the end user.
That’s why we say: real protection starts with insight. We are happy to help determine the protection level needed for your application.